Social Contribution Activities
Community Contributions
NST rolls out the Japan-India Institute for Manufacturing (JIM) initiative to support human resources development (HRD) in India
Commitment to HRD
Our group company Neemrana Steel Service Center India (NSSI), which runs steel sheet processing business in the Indian state of Rajasthan, has long been committed to employee training. Such training is provided through the lecture course called “DOJO” and on-the-job training (OJT) in five departments: coil centers, press working, quality control, maintenance, and warehousing and shipping.
Certified as a JIM
Against this background, we endorsed the concept of “Japan-India Institute for Manufacturing (JIM)*,” an HRD project launched at the initiative of the Ministry of Economy, Trade and Industry of Japan and the Government of India. This is how we initiated our own initiative with a view to obtaining certification as a JIM. The aim is to train not only employees at NSSI but also other local young people who will support the future of India's manufacturing industry as part of our mission to contribute to society.
In January 2023, we accepted ten local training participants and launched an education program aimed at teaching knowledge and skills in manufacturing steel products. This led to the JIM certification in April 2023.
- *JIM is a HRD support initiative based on the Memorandum of Cooperation on the Manufacturing Skill Transfer Promotion Programme , which Japan and India signed in 2016. The goal is to train prospective shop floor leaders at Japanese companies in India by providing the Indian youth with the opportunity to learn skills in Japanese-style manufacturing and the ideas behind it. The target is to train 30,000 manufacturing personnel over a period of ten years.
Components of the education program
First Step: DOJO
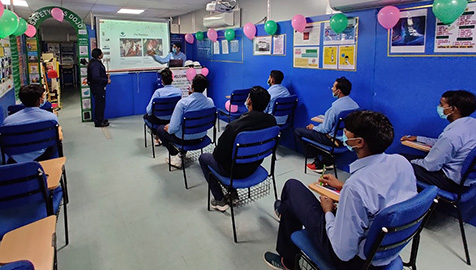
As the first step, the JIM at NSSI provides the lecture course called “DOJO” (a training hall in Japanese). DOJO encourages training participants to take the time to learn basic knowledge on quality control, manufacturing, maintenance, warehousing, and shipping, as well as Japanese-style thinking behind these processes, while stressing the importance of giving top priority to safety. Training participants learn in DOJO for 11 days first, followed by OJT. While they are at OJT, they also learn in DOJO every Friday in a one-year cycle.
DOJO was created in January 2017 to provide better employee education than ever before. Since then, DOJO has undergone a series of improvements through learning by doing. In June 2018, the course was expanded to enhance its content. In December 2022, it was updated to cope with the expanded lineup of products.
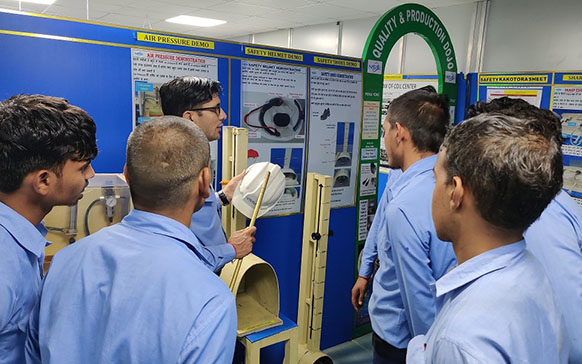
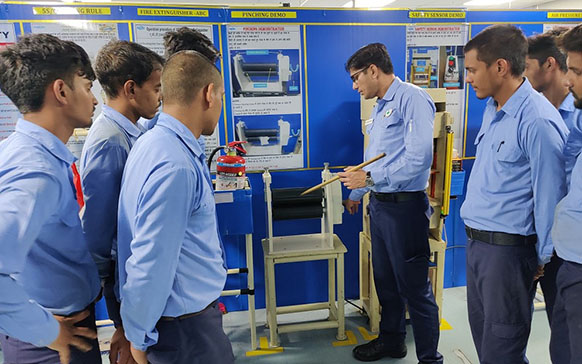
Learning skills through OJT
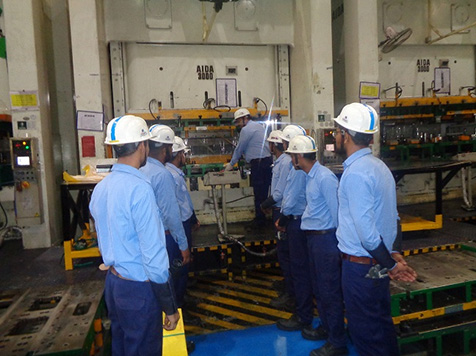
In OJT, participants are given instructions on how to handle machinery on the shop floor. They thus learn how to operate machines according to operation standards while checking important points in the process from the starting of such machines. As OJT progresses, participants get used to such operations. Not to become complacent, they are taught the importance of operation standards again so that they understand the value of strictly following set rules. By repeating this process, they gradually acquire skills. They may be allowed by their functional managers to stand alone.
What local participants have to say
“We learn many new valuable things from the training at NSSI. In the lecture course, we learn the basics. In OJT, we learn how to operate instruments and machines on the shop floor and acquire related skills every day. We believe that this training is a great help for our future and a good opportunity to improve our skills.”
“Thanks to this training, we have started a new lifestyle. Our lifestyle used to be such that many members get up late in the morning. Now that we have joined NSSI, we get up and go to work on time. Our teachers and senior colleagues have taught us about good habits.”
“We enjoy everyday work and learn how to lead a healthy life. Now, we spend far less time on a smartphone and have plenty of sleep. We learn a lot about such off-duty things as well.”
“In addition, NSSI puts safety first. We, the members, always discuss operations that give top priority to safety. We have a very good work environment. We are grateful to NSSI and the JIM for having given us this opportunity.”
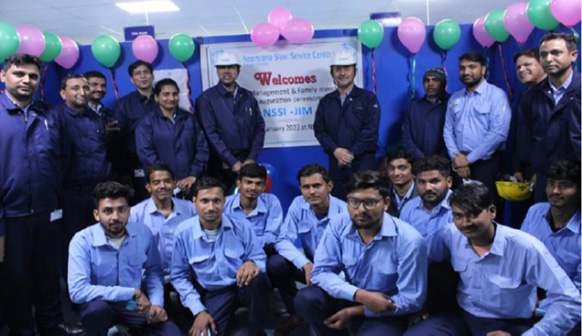
JIM certification ceremony
On April 27, 2023, the Ministry of Economy, Trade and Industry (METI) held a ceremony in one of its meeting rooms to celebrate the METI certification of us as a JIM. Koshikawa Kazuhiro, Senior Managing Executive Officer at NST attended the ceremony. Also attended were Mr. Nakatani Shinichi, Senior Vice Minister of Economy, Trade and Industry; Mr. Tokiwa Mitsuo, Deputy Director-General for Trade, Economic Cooperation and Export of Agriculture, Forestry and Fishery Products ; and Mr. Sibi George, Ambassador of India to Japan.
<Address by Koshikawa at the ceremony (excerpts)>
“We have long believed that we need to contribute to India through developing local human resources while doing business in the country. This is why we endorsed the basic policy behind the Japan-India Institute for Manufacturing project. We are committed to moving this initiative forward with continued support of the authorities concerned, including relevant agencies in India and METI.”
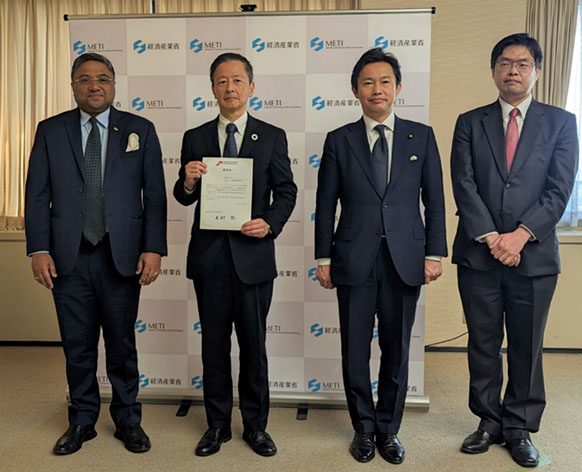
(From left to right) Indian Ambassador George, Senior Managing Executive Officer Koshikawa, METI