Safety, Quality Control, Compliance
Among the various risks, NST focuses its attention on further strengthening company-wide efforts concerning risks related to safety, quality, and compliance. It includes cooperative efforts with the business and functional divisions to identify the critical risks that could have a serious impact on management, and to examine and implement measures to eradicate them.
Initiatives for Safety
Steel Division (Technical Support & Safety Management Department)
The Steel Division aims for zero major accidents and the elimination of lost-worktime and non-lost-worktime accidents. It is carrying out independent safety activities focusing on the three priority measures listed at right.
- Priority measures
-
- 1.Improved safety awareness level and full observance of safety rules
- (1)Identification and elimination of unsafe actions that persons are unaware of
- Identification of unsafe actions from a workplace perspective
- Deployment of voluntary safety activities among operators (small group activities, calling out to one another)
- (2)Training and instruction to instill safety rules in employees
- Review to create work standards where safety rules are clear and complete adherence to them
- Improving understanding of safety rules and hazard sensitivity (KYT, training using studies of similar accidents etc.)
- (3)Continued identification and reduction of hidden risks
- (1)Identification and elimination of unsafe actions that persons are unaware of
- 2.Continued extreme 2 heat countermeasures
- Workplace environmental improvements (wearing air-conditioned clothing, installation of spot coolers, etc.)
- Review of rules for times of extreme heat (break intervals, number of breaks, break locations, etc.)
- Reasonable work plans, workplace culture that prevents unreasonable work (verbal communication campaign, etc.)
- 3.Continued autonomous management activities for chemical substance regulations
- 1.Improved safety awareness level and full observance of safety rules
Industrial Supply & Infrastructure Division (Industrial Supply & Infrastructure Planning Department)
- Priority measures
-
- 1.Follow-up by checking the progress of voluntary safety audits
- Support was provided to enable each manufacturing site to establish and further strengthen a system in which it can continue its own efforts to identify and resolve improvement issues based on voluntary safety audits.
(Note) Measures to prevent contamination by foreign matter in processed foods in the Foodstuffs Division is listed in its initiatives for quality control.
- 1.Follow-up by checking the progress of voluntary safety audits
Initiatives for Quality Control
Steel Division (Technical Support & Safety Management Department)
In parallel with system implementation by the DX Promotion Department, the Division is reducing the numbers of check items and carrying out thorough double-checking to prevent human errors.
- Priority measures
-
- 1.Double-checking through monitoring of the sales department’s order entry operations
- In order entry and processing order operations at sales departments in Japan, identify cases of corrected order entries, verify the reason for correction, check the conditions of double-checking, and apply them to work standards.
- Verify order entry operations and optimize work standard documents at sales departments of overseas subsidiaries.
- Create masters and carry out correction of work methods (such as uploading Excel files) with the aim of eliminating reliance on human resources in order entry operations.
- 2.Support for improvement of priority management items in affiliated companies
- Study milestones toward sharing and reducing quality risks.
- Continue utilizing bar codes and automatic transmission with the aim of eliminating reliance on human resources.
- 3.Activities to support sales and affiliated companies
- 1.Double-checking through monitoring of the sales department’s order entry operations
Industrial Supply & Infrastructure Division (Industrial Supply & Infrastructure Planning Department)
- Priority measures
-
- 1.Thorough guidance and continuous monitoring of key suppliers in the Mobility Business Department and the Functional Materials Department
- 2.Establishment of a technology quality assurance manager in the division, carrying out quality action for car manufacturers and other customers, and constructing a quality management system for each supplier
Foodstuffs Division (Food Quality Assurance Department)
In the Food Quality Assurance Department, we are carrying out measures against foreign matter inclusion (including allergens) in processed foods.
- Priority measures
-
- 1.Stringent selection of processing plants, and thorough analysis and tracing of ingredients, including sub-materials
- 2.Strengthening of recall training on the production side
- 3.Engagement of insurance to insure against damages in cases when responsibility is not clear
- 4.Expansion of support for human resources development (further improvement of safety measures through the use of highly skilled employees)
DX Promotion Department
In quality control, operations requiring manual operation cannot be zero risk. At NST, the DX Promotion Department addresses the challenge of eliminating this quality risk by digitalizing operations across all manufacturers, distributors, and customers.
- 1.“N-SCM” integrated inventory management system
- Automation of inventory management in repeating transaction fields in order to produce faster responses to changes in conditions, and to prevent shipping problems caused by missing materials or wrong materials.
- 2.“SPOD” improved order entry system
- Standardization of order placement operations and strengthening of the check functions to improve accuracy and efficiency, and to eliminate human errors.
- 3.“EXCS®” new coil center system
- Updating and consolidating the core business management systems at NST subsidiary coil centers
- ※All three systems began full-scale operation in fiscal 2023, and we are continuing to expand the functions, increase the number of product categories, and increase the number of sites where they are used. In addition, we are conducting comprehensive development aimed at further full digital conversion of trading company operations by linking with the “NST Business Online” information exchange portal that has begun full-scale operation.
Initiatives for Compliance
Basic approach to internal control systems
NST has clarified its basic attitude to emphasize compliance in accordance with the Corporate Philosophy, Management Principles, and Employee Code of Conduct. NST implements and operates internal control appropriately, further strengthens its corporate governance, endeavors to ensure “compliance with laws and ordinances,” “reliability of financial reporting,” and “effectiveness and efficiency of operations,” and aims to improve them continuously.
- 1. Internal control in business execution (three defense lines)
- NST has constructed and maintains an internal control system based on three defense lines: the first defense line comprised of departments engaged in sales, etc.; the second defense line including functional departments, mainly comprised of the Corporate Planning & Administration Division and its departments as well as each sales planning department; and the third defense line comprised of departments engaged in internal controls and auditing.
- 2. NST Group’s internal control systems
-
NST and each subsidiary shall establish internal regulations to ensure the appropriateness of business in accordance with the Corporate Philosophy, Management Principles and Employee Code of Conduct, and hold business strategy in common based on the business characteristics of each division and subsidiary. Thus, NST and each subsidiary shall operate as a single group.
Each Executive Director, Executive Officer and general manager in NST and the directors of each subsidiary shall have employees fully understand the Corporate Philosophy, Management Principles, Employee Code of Conduct and regulations, and perform self-checks and monitoring. The department in charge of the management of each subsidiary shall operate the subsidiary appropriately in accordance with the “Subsidiary Management Regulations,” the “Subsidiary Management Standards,” etc., under the responsibility of the Executive Officer who supervises such department. NST shall dispatch its Executive Directors, Executive Officers or employees to subsidiaries as Directors or Audit & Supervisory Board Members in case of necessity, and ensure the appropriateness of business execution.
The Internal Control & Audit Department shall cooperate with functional departments, provide instruction and support to prepare the internal control system at NST and its subsidiaries, share information between the Company and subsidiaries, and aim to fulfill the requirements of internal controls. It is also conducting awareness surveys and e-learning related to internal controls for all employees of NST and affiliated companies in Japan and overseas, and is working to improve awareness of internal controls.
Internal reporting system (Compliance Hotline)
NST has established and operates the Compliance Hotline for employees and others at NST and its subsidiaries as a contact for internal reporting and consultations related to risks in the conduct of our operations. It protects confidentiality for reporting, and protects whistleblowers from retaliation. Beginning from June 1, 2024, in addition to the existing contact for internal consultations, the Compliance Consultation Room established by Nippon Steel is also available. A contact system based on contracting to an outside party was also established so that whistleblowers can report and consult with confidence, and we are working to expand and continually improve this system.
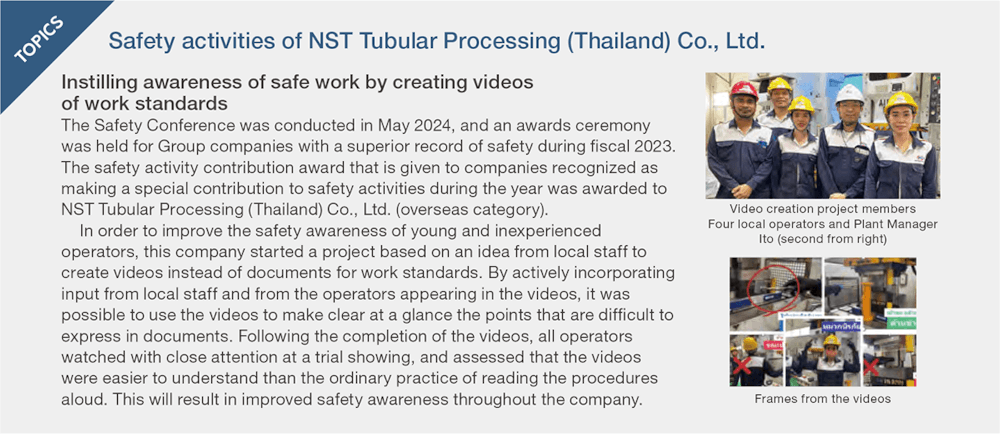